3D Scanning
No two logs are alike. As each log enters the Green Mill, it passes through a laser scanner at speed and is 3D modelled. This data is then passed down the line and used to generate a cutting plan in real-time, slashing the time it would otherwise take to make fateful decisions.
The Linck Line
From the control room you'd be forgiven for thinking we're launching a rocket, and in a way that's somewhat true. Log after log make their way along the Linck Line as fast as an Olympic walker, and so our operators must have their finger on the pulse.
Route, cut, scan, repeat
We don’t saw immediately. Instead, a symphony of routers carve out four flat faces and corners forming a plus-like profile which is again scanned to ensure ongoing precision. At this point, the first 2 planks 'fall off' the sides, the log is rotated, scanned again, and 2 more sides fall off. This pattern of scanning and cutting is repeated several times until the log is no longer.
The end of the line
Once the Linck line has done its thing, we're left with a jumble of sideboards and planks. These travel the remainder of the line before joining their log-mates for a bit of a conveyor party before being separated into groups according to their dimension.
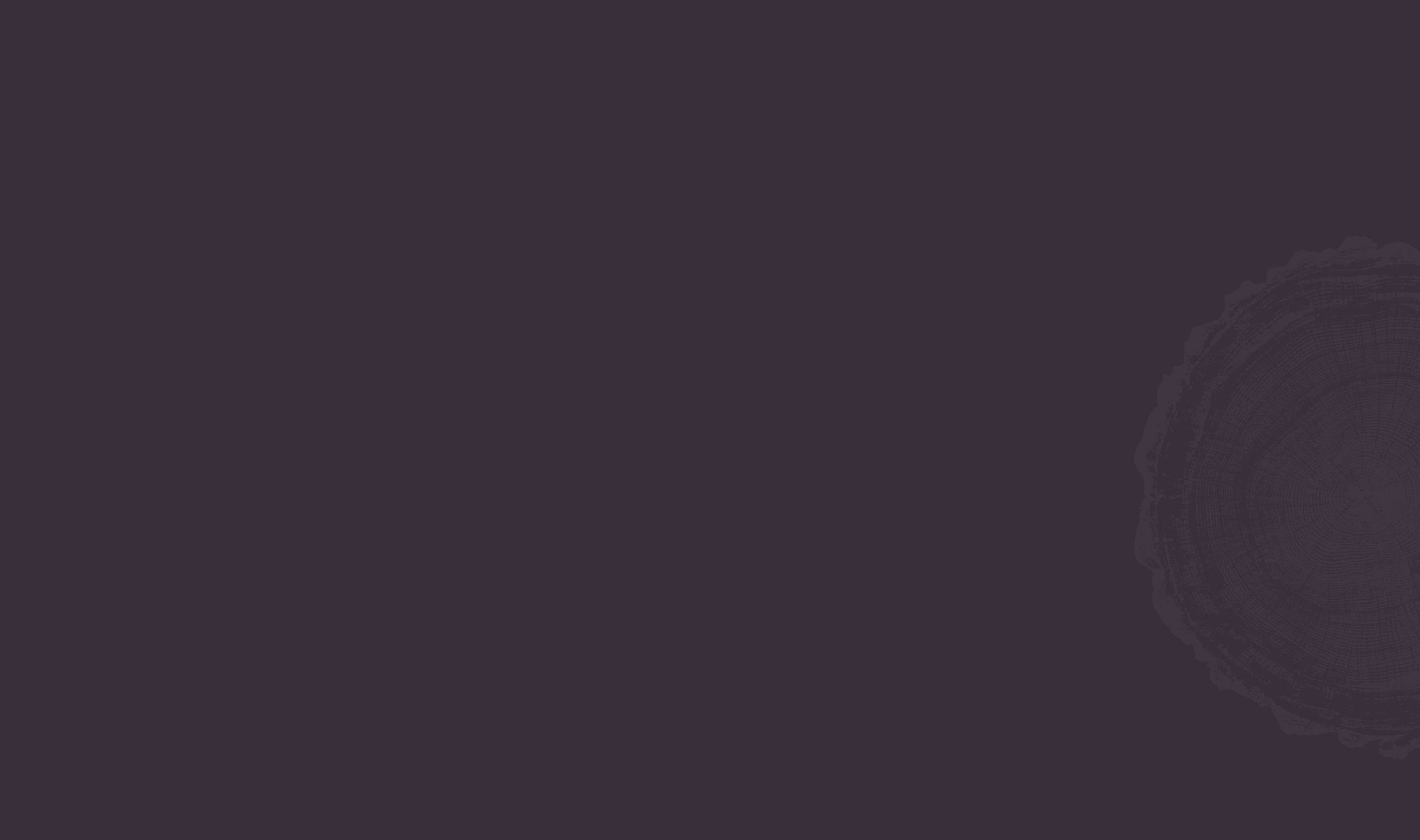
sustainability in focus
The cutting room floor
It gathers a lot of dust... err, saw dust... and wood chip! Despite improvements in technology, only about 50% of a log goes on to become 'bread and butter' product. A labyrinth of belts catch 'by-product' and whisk it away. It then goes on to become a myriad of industrial and household products.
Onward and upward
It’s more efficient for us to move boards and planks laterally. After ascending to a sorting facility the sound becomes reminiscent of a ten-pin bowling alley as boards begin to fall into bins sorted by dimension.
Sorting
At this point we could have a genuine jigsaw puzzle on our hands, but fortunately the process of sorting is automated. Every plank has been printed with an identifying product code, letting us know its dimensional and density data and allowing us to cook evenly in the Kiln.
Packed for the kiln
After sorting, the final step is laying strips and bundling everything up into a kiln 'charge.'
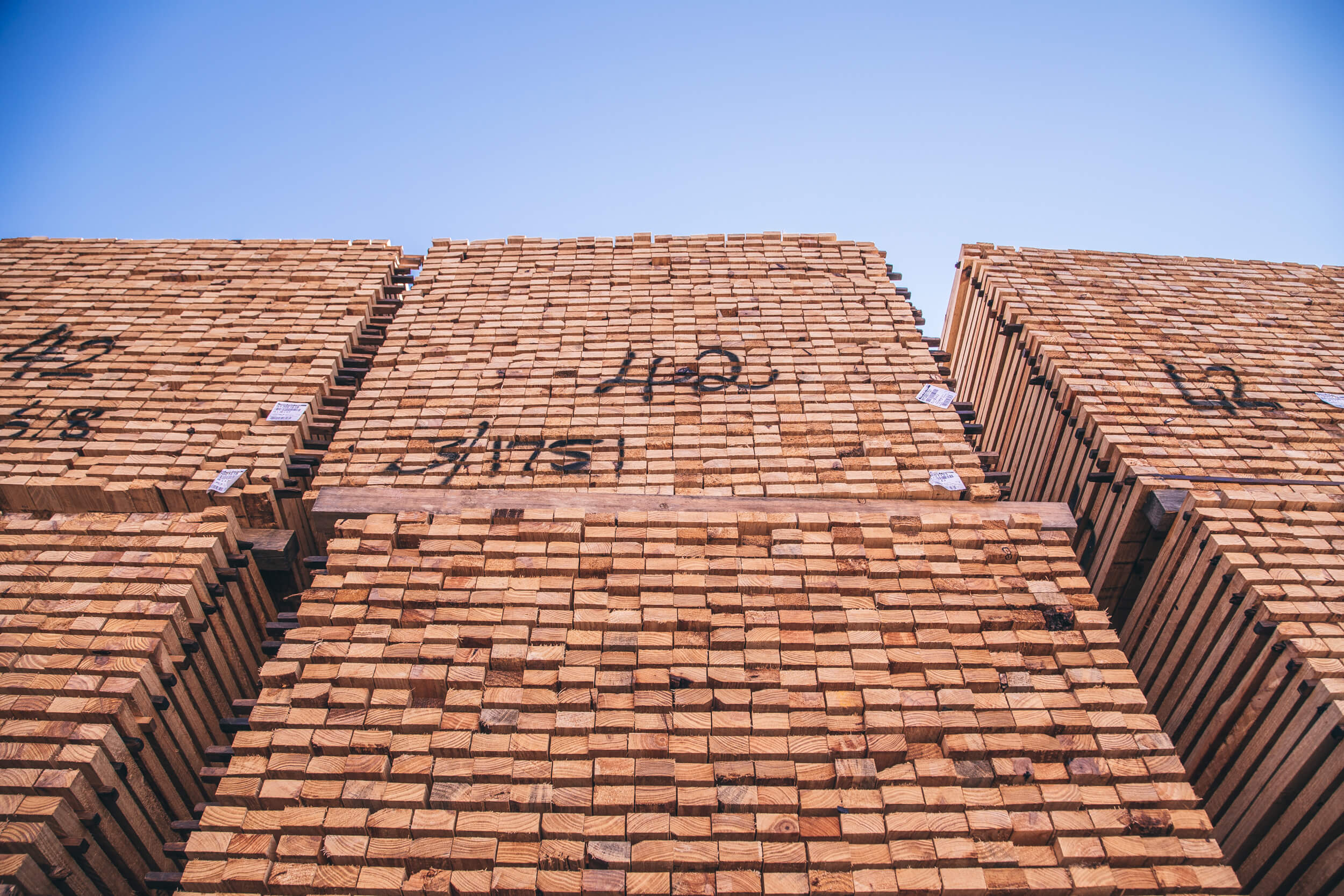