A weighting game
Every kiln 'charge' is weighed down with a slab of heavy metal which prevents the timber from changing shape as it releases moisture. Once a charge is ready, it's loaded into place with the help of a kiln car.
Turning up the heat
The kilns are heated by a network of pipes that ferry hot oil back and forth between the heat plant and our 7 kilns, aiming for a consistent internal air temperature of 190ºC to most efficiently remove moisture. Clouds of white steam billow into the air as cool dry air is fanned from one end to the other, periodically reversing direction to ensure even drying throughout.
3 hours later
After a stint at 190ºC, a standard kiln charge is ready to begin a phase of equalisation. When doors to the kiln open, a thick blackened residue of vaporised tree sap is left as a reminder of its time with us.
sustainability in focus
Powered by by-product
It takes a lot of energy to power a kiln, but instead of burning coal like in a steel smelter, we power our kilns with bio-fuel pellets made from our own sawdust. It's just one of the factors that add up to timber having one of the lowest embodied energies of all construction materials.
Durability takes time
Some argue it's an art, but our team argue they have it down to a fine science. Either way, there's no argument the kiln-drying process is the biggest bottleneck in any mill, and for many of our competitors the temptation to rush the process is too great. We take that little bit extra time to ensure we get the science right... because that little extra care means a whole lot extra durability.
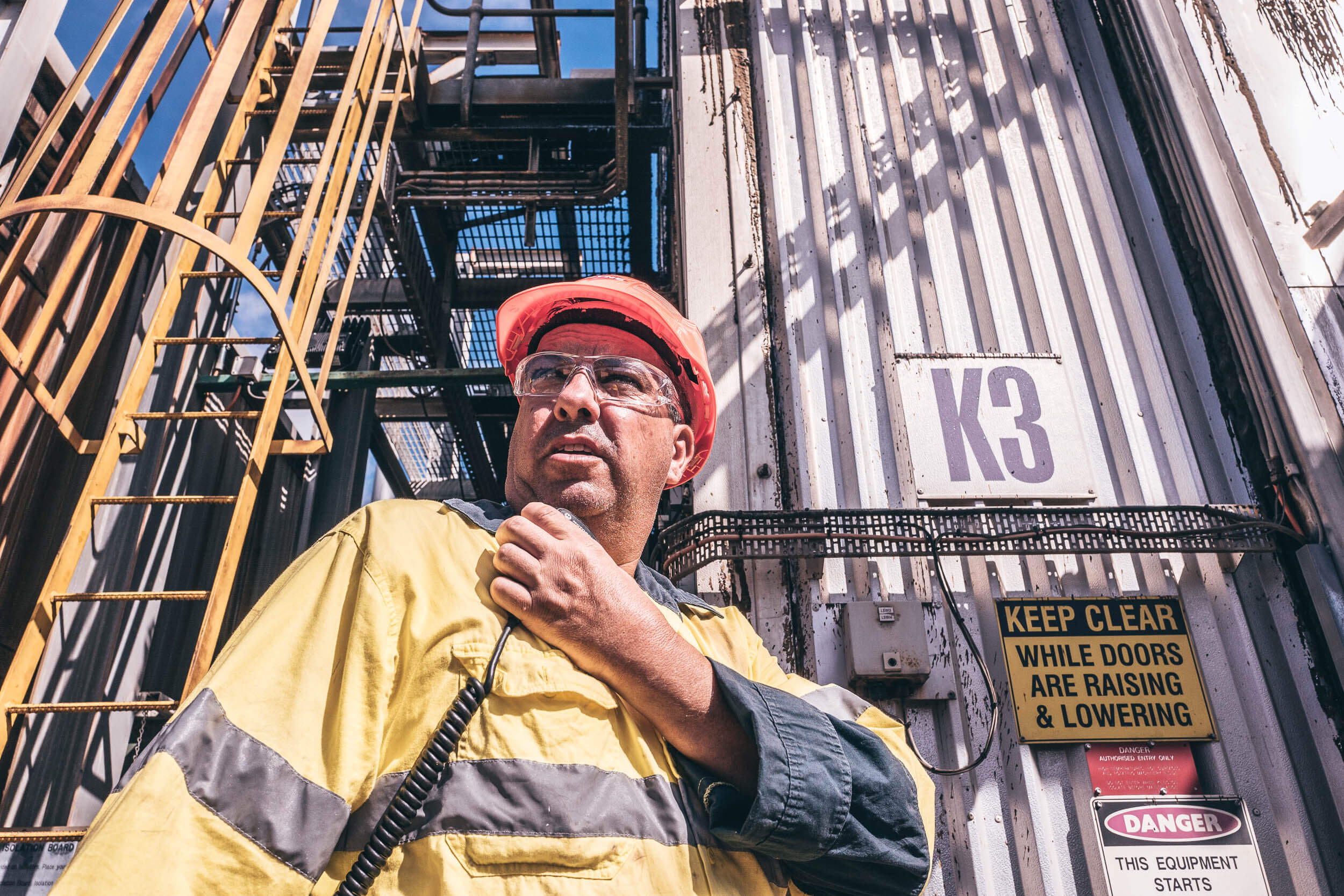